If helmet maker Giro has its way, landfills will be filled with a lot less Styrofoam from bike helmets in the near future. Last month, the company unveiled the first helmet made from compostable foam and recyclable plastic. Called the , the commuter lid will hit shelves this fall at a retail price of $50.
鈥淲e have been researching alternative materials for quite some time as part of a strategic initiative to lead innovation in head protection,鈥 says Christopher Pietrzak, director of advance concepts at Giro. 鈥淲e consider sustainability to be an important factor in the evolution of helmets.鈥
Helmets have been slow to evolve, environmentally speaking. Most modern helmets are still built around a petroleum-based foam called expanded polystyrene, or EPS, which doesn鈥檛 biodegrade. The Silo, on the other hand, utilizes a new type of foam derived from plant matter鈥攊n this case, corn鈥攃alled expanded polylactic acid, or E-PLA, which can be composted.
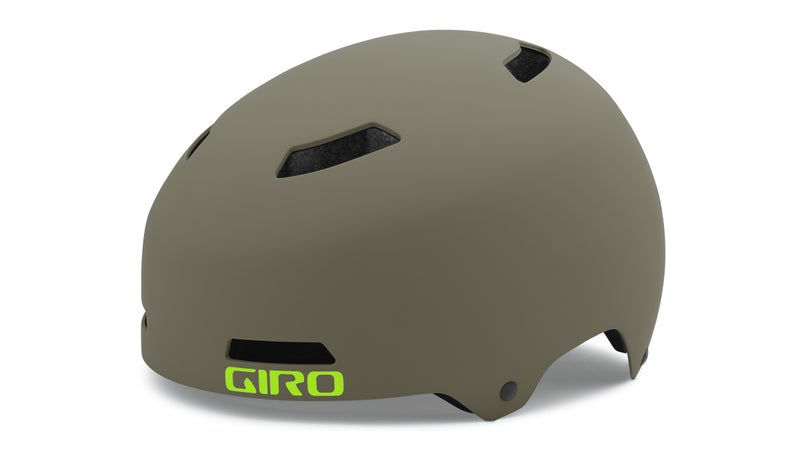
Using this new foam in helmets for the first time required four years of development and testing. To meet safety standards, the company needed to design a higher grade of material than the E-PLA used for other applications, like packaging or construction materials. And getting it to biodegrade at the right time (not too soon!) requires a just-right combination of moisture, temperature, pressure, and time, a process that also required extensive testing.
鈥淓very step of the manufacturing process, from stabilizing the foam, to bonding the foam with other components, to final testing for performance and quality, requires a significant investment and expertise to ensure that the final product meets the same stringent standards for performance, reliability, and quality as a helmet with more conventional foam,鈥 says Pietrzak.
Giro also performed years of testing on the helmet in its in-house research facility at its headquarters in Scotts Valley, California, near Santa Cruz, where researchers conduct聽more than 50 different types of tests to simulate an array of impacts. The helmet was also聽tested for certification at an independent lab. The company hopes to incorporate the foam in more of its helmets in the near future, but that will requiring shaping it to more complicated molds. Giro will聽need to utilize a process it calls InMold, which uses steam and pressure to fuse聽expanded foam beads from the liner with the polycarbonate shell in a mold.
Pietrzak says he expects riders to use the helmet for three to five years, roughly the lifespan of a traditional cycling helmet. (Like all single-impact helmets, it should be replaced sooner if it sustains an impact.) When you鈥檙e done with the helmet, you can recycle the shell and bury the foam in your backyard, where it will degrade over a long period of time. You can鈥檛 compost this foam with your coffee grounds鈥攊t won鈥檛 break down fast enough鈥攂ut you can send it to an industrial composting center. (Check with your local center, because many won鈥檛 accept anything but food remnants.)
鈥淲e applaud Giro鈥檚 efforts to create bike helmets that use more sustainable materials and manufacturing processes,鈥 says Doug Peterson, category merchandise manager at REI, which will stock the Silo this fall in 36 stores and online. 鈥淲e always want to give our members the opportunity to try interesting new technologies, particularly those that align to our sustainability goals and practices, and look forward to seeing how this helmet is received.鈥
So why all the time and money to release a $50 helmet? 鈥淪imply put, it鈥檚 the right thing to do,鈥 says Pietrzak. 鈥淗elmets should continue to evolve, like any product, and reducing the environmental impact of our helmets is a goal that aligns with who we are as human beings and employees. We have a lot invested in Silo, and it will take time to recoup that investment, but it鈥檚 worth the risk. We want to lead with new ideas that can make things better.鈥