On a snowy day, back in February 2012, Dr. Gary Selwyn was busy in his kitchen in Santa Fe, New Mexico. He wasn鈥檛 fixing up a stew. Instead, he was blending hydrocarbon-based monomers, cross-linkers and polymerization initiators.
The chemist, formerly at Los Alamos National Laboratory, was used to big challenges and this one was no different. He was preparing a formula that had the potential to disrupt the textile industry for the next 100 years鈥攁 replacement for perfluorinated fluorocarbon (PFCs).
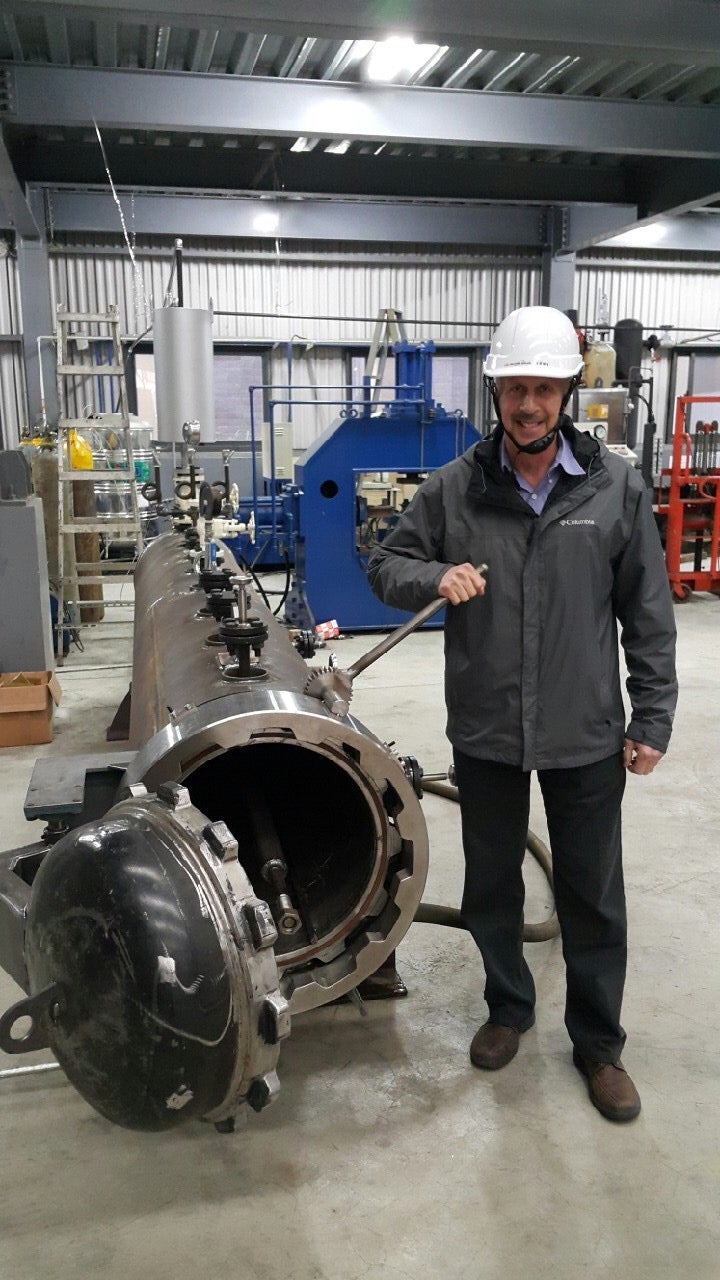
PFCs are chemicals commonly found in Durable Water Repellents (DWRs) on performance textiles. PFCs have been used extensively for the last 50 years. But new data and mounting lawsuits underscored the need for this to change. In conventional textile finishing, fabrics are pulled through a water-based 鈥渂ath鈥 containing the harmful PFCs. PFCs are persistent, so when the bath is flushed, the same PFCs end up in the groundwater and soil. Then, those same carcinogenic PFCs end up inside our bodies, where they can lead to cancer and birth defects.
Dr. Selwyn was determined to find a new way to create a PFC-Free finishing technology that offered superior water repellency. He found that water-free finishing was the way to go. The future of dry finishing technology was just being born.
Around the same time, Greenpeace issued a radical challenge, calling for outdoor companies to stop using harmful PFCs in their Durable Water Repellent (DWR) treatments.
It was music to Selwyn鈥檚 ears, because his kitchen experiments had produced a major development: a radical new finishing technology that not only met the Greenpeace challenge, but outperformed fabrics treated with the traditional “dirty” DWRs. Even better, it used no water.
Selwyn鈥檚 new company Green Theme Technologies (GTT) continuously refined and patented this new innovation.
Fast forward four years to the winter Outdoor Retailer (OR) show. Selwyn鈥檚 thermal, dry finishing technology is now producing high quality, finished fabric swatches. Selwyn meets up with Martin Flora at the OR show and Martin introduces him to Ryan Chen, who has a small textile operation in Taiwan. There, the three planned the emergence of , a combined East/West company that works together with GTT to bring newly-named 鈥淎quaVent鈥 technology to market as an environmentally responsible PFC-free and water-free finishing technology.
Extraordinary Performance Test Results
Selwyn鈥檚 initial goal was for AquaVent to withstand 50 machine wash cycles and still repel water under the industry standard AATCC 22 Spray Test. He was thrilled when it far surpassed that goal. “It achieved 100 washes with a spray rating of 100, and this was unheard of,” Selwyn said. Essentially, AquaVent proved immune to laundry as well as wear and tear.
The AATCC 22 Spray Test resembles the gentle watering of flowers from a garden bucket for 30 seconds. Since this is unlike actual rain, it provides an unrealistic test of water repellency performance. Undoubtedly, the best rain simulation is the Bundesmann Water Repellency Test, where water hits the fabric with a force roughly five times that of a cloudburst, simulating wind-driven rain. Added to this are moving rotors to simulate wear. In total, it is estimated to be 200 to 1,000 times tougher than the AATCC spray test.
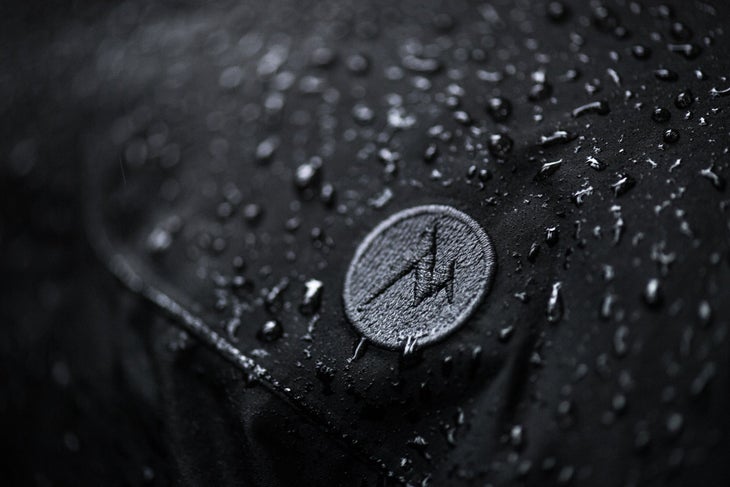
Where the AquaVent technology really proves its mettle is with the Bundesmann Test. In this test, a number of key metrics are collected including the rating of visual repellency (from 1 = fully wetted to 5 = perfect), the percentage of absorbed water and the amount of water penetration through the fabric. Traditional finishing generally scores well under 2 with many that fail in the first one minute of the ten-minute test. AquaVent fabrics score over 4. In the real world, this is the difference between a jacket wetting out and feeling damp after six months of use, and one that continues to bead water like new indefinitely.
Water-Free Is the Magic Bullet
The secret behind such performance is the AquaVent dry-finish process. While virtually all other textile companies use wet-finishing, the AquaVent technology is an entirely new, water-free platform technology. It uses high-pressure gas to push the chemistry into the fabric and then thermally polymerizes the chemistry fusing the polymer with the fabric’s fibers on a molecular level. This strong bond means the finish is baked into the garment and won’t wear off or wash out. “You’re no longer just coating the fabric,” Selwyn said. “You’re overcoming factors like surface tension and the compressive nature of the knit and you’re able to get that penetration (deeply) into the fabric.”
What’s more, because the process behind his breakthrough dry finish technology doesn’t use water, it could clean up the textile industry, the second largest user and polluter of water globally (behind oil). The process is so groundbreaking and disruptive, even its inventor is watching its potential unfold. “I think we’ll be learning about it 50 years from now. We’re changing the way that textiles are made.”
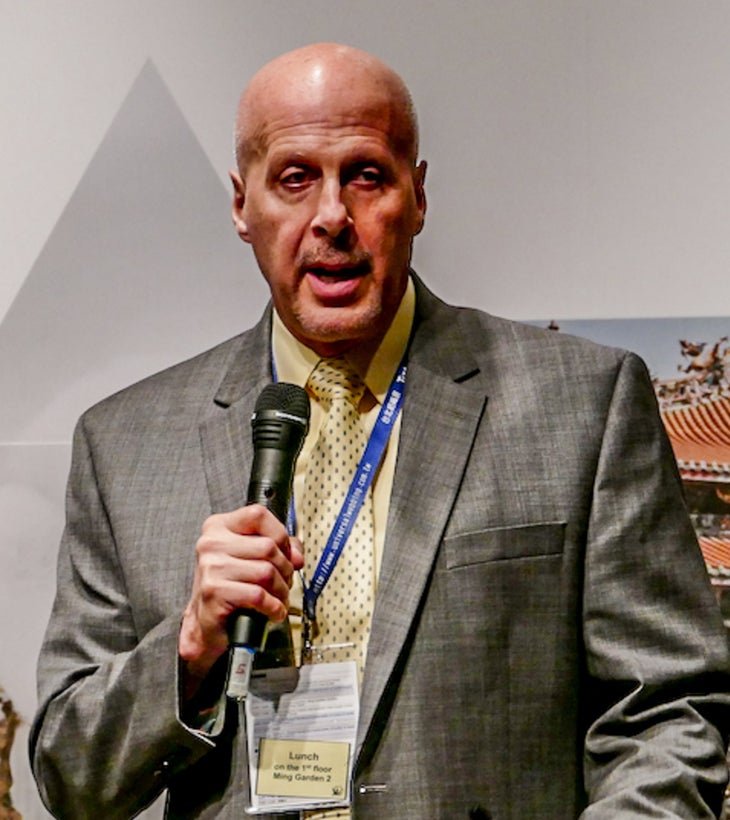
Selwyn has seen this kind of profound technological advance change an industry before, because of a switch from ‘wet’ to ‘dry’ technologies. “I came from the semiconductor industry. In the ’80s, that industry was water-based. They dipped electronics into acids but then they changed course and began using a plasma鈥攄ry based鈥攑rocess. This allowed for miniaturization and high-density circuits that now power laptops, cell phones and microwave ovens.”
Early Aquavent Adopters
The performance of Aquavent caught the eye of designers at Marmot, who partnered with Green Theme International to use the technology in its EVODry rainwear, part of the brand’s own push for more sustainable apparel. The collection hit REI stores in February 2018, and Marmot says its EVODry jackets will protect against heavy rains for 24 straight hours. Backpacker recognized the Eclipse Jacket as one of the year’s most innovative pieces of gear and Gear Junkie awarded it Best in Show at 2018 Outdoor Retailer Winter Market.
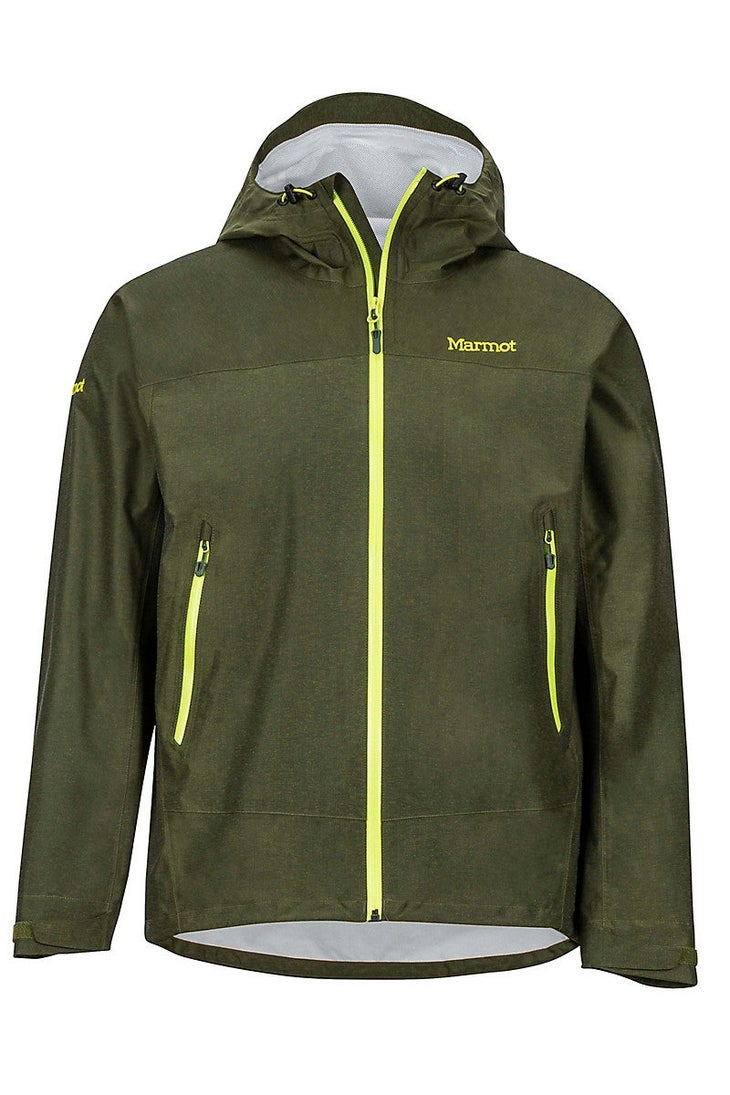
For spring 2019, Marmot has expanded its use of the Aquavent technology. (It will be on display at Outdoor Retailer Summer Market this month in Denver). “Even when you’re just out walking you still need your pants to perform if it starts to rain,” said Claire Gibson, Marmot鈥檚 sustainability manager. “Working with GTI and our mills, we were able to find fabrics we felt were very on-trend and have been able to elevate our sportswear category.” Marmot is also using the tech in some fleece pieces. “There’s some different performance features when you use it on knit fabrics, but it definitely does help for protection in the off chance that you encounter precipitation,” Gibson said.
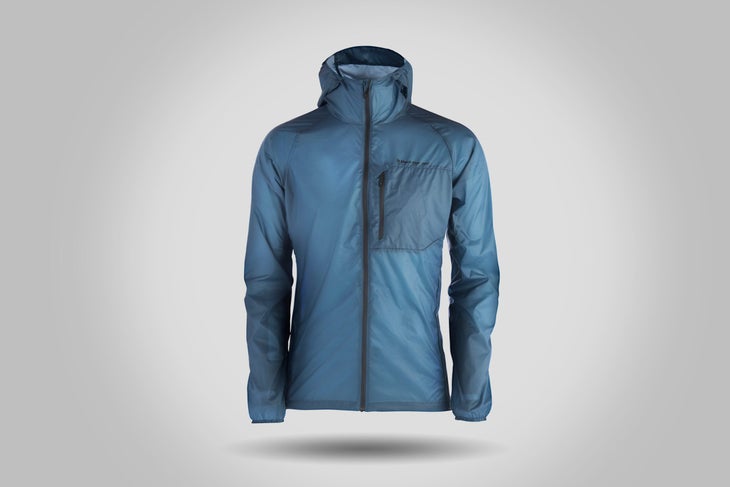
Black Diamond is the latest brand to partner with GTI, and its light-and-fast Distance Wind Shell, slated for spring 2019 and also being unveiled at Outdoor Retailer, was designed around the needs of sponsored athlete Joe Grant, whose trail running feats include a series of mountain ascents. “The GTI technology allows Black Diamond to achieve long-lasting water protection from both external and internal sources, cutting dangerous evaporative heat loss through wind exposure, while maintaining the lightest weight possible,” said Trent Bush, vice president of apparel at Black Diamond Equipment.
Bush says he was eager to get the shell to market while also testing the fabrics for other applications, from apparel to tents. “While [Aquavent] is an important outcome of GTI鈥檚 patented process, it is not the only one, just the first,” he said. “From a product-creation perspective, this is a dream come true. We can now manipulate variable performance and possibly aesthetic parameters at a totally new level.”
You Can’t Pollute What You Don’t Use
What Bush alludes to as a wide-open technology for new products, Green Theme sees as the path to the future: the most differentiating thing about Aquavent wasn’t that it is PFC-free, but that it鈥檚 water-free. The zero hazardous discharge process was groundbreaking. Not just better, but revolutionary. It was a game-changer for the industry. That became the inspiration for Green Theme.
In fact, it’s been through testing with partner brands, like Marmot and Black Diamond, that the textile industry continues to discover more benefits of the new technology. For instance, the Aquavent treatment keeps clothes cleaner longer because the polymer finish is not oleophilic, as with some other PFC-free finishes. Also, bonding of the polymer to the fabric improves the life cycle of the garment by preventing pilling and toughening fibers to withstand more washes and wear. Better laundry durability means fewer chemicals are washed off.
“As a company, I think we鈥檝e opened the door to what the future can look like. We don’t separate the mission of taking care of the planet from innovation,” said Green Theme鈥檚 Martin Flora.
Unlike a third of the PFC-free DWRs on the market, Green Theme’s dry process excludes the use of palm oil. Vegetable oils like palm and corn became a common substitute oil in the race to create PFC-free DWRs, since they had some natural repellency. However, they came with their own set of problems. On paper, palm oil sounds sustainable, but it has created economic incentive to mow down tropical rainforest that are home to endangered species, and plant palm tree farms. Plus, oils love mixing with other oils, resulting in an oleophilic finish.
Because the AquaVent technology uses a sealed chamber pressurized by gases there is no waste stream. Another advantage is the process allows for a cocktail of fabric treatments at once, so odor-resistant or flame-retardant qualities can be added without taking the fabric through an additional chemical bath.
Eliminating PFCs, avoiding palm oil, and reducing chemicals are all big steps in terms of sustainability, but the largest impact could come from Green Theme鈥檚 water-free process.
For apparel brands and textile manufacturers, this may be an “adapt or die” moment. Textile production is a dirty business: textile companies use roughly half of the world’s chemicals and generate one-fifth of the world’s industrial water pollution, according to the Natural Resources Defense Council. Most textile mills are in countries with poor pollution treatment and they often face a critical shortage of fresh water. Drought-stricken Sri Lanka, India, and major cities in China are already calculating a Day Zero of access to clean water. Wet-finish mills have operated for more than a century but are increasingly unsustainable.
“If you look at a lot of the mills, they know they need to clean up, but they’re still holding onto the wet-finish process, which uses chemicals and lots of water, both of which are expensive,” said Green Theme鈥檚 Brian LaPlante. “Our sell is that adopting the dry-finish process will save [mills] money in the long run because they will use less. Margins have a way of changing mindsets.”
Next Steps
Green Theme Technologies and Green Theme International are in the process of merging together and joining forces to deliver new technologies and innovations in water-free finishing of textiles, not just for performance outdoor wear, but also for fashion apparel, footwear, automotive textiles, military applications, marine and home-based textiles. That 鈥渟oup鈥 that Selwyn started in his kitchen several years ago will continue cooking for some time and has the aid of multiple, visionary-minded teammates.